A comprehensive guide to aluminium welding technology.
The Complete Guide to help you choose the Best Welder
by the Real Experts of Equipment for Repairs and DIY Activities
Aluminium is one of the most sought after materials by both DIY welding enthusiasts and professionals. What are the characteristics that make aluminium such a special metal?
- Lightweight
- Softness
- Oxidation resistance
- Durability over time
1. Introduction
Welding aluminium is not an easy task. Aluminum is a light metal which melts at relatively low temperatures, while producing an oxidation layer which instead melts at higher temperatures. Due to the “low” melting temperatures there is a high risk, if you are not experienced, of “piercing” the aluminium foil that is being welded, especially when working on thin parts.
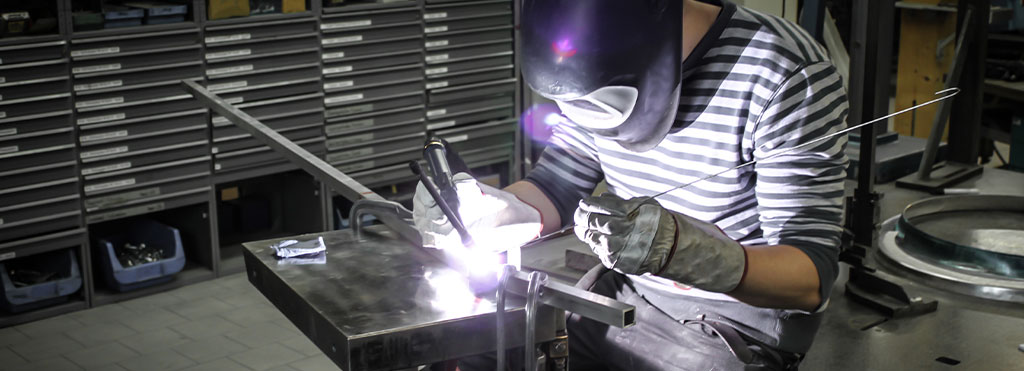
A further challenge lies in the fact that aluminium does not change colour when it is melted, making it difficult for the untrained welder to identify the exact moment of melting. Therefore, no beginner or inexperienced user should attempt to weld aluminium, as it takes adequate preparation and a good deal of experience.
The brittleness of the breaking points of this metal is certainly a major obstacle to its processing. In fact, aluminium was once regarded as more valuable than gold, being rare to find in nature unless extracted from other elements, and for its qualities:
- high corrosion resistance
- high thermal conductivity
- high ductility, plasticity and malleability
- reduced radiant power
- it does not produce sparks
- weldability
Aluminium can be welded with either TIG or MIG wire welders
2. Aluminium TIG welding
In the previous purchasing guide for the best welder, we explained how TIG welding is performed using a non-consumable tungsten electrode and with the aid of gas. Read more about how TIG welders in the main purchasing guide.
When welding aluminium with a TIG welder, ARGON gas is required. Before starting the welding process, it is necessary to clean the parts to be welded and the filler material with acetone, and then run them under water to remove the protective layer that the aluminium has created by coming into contact with air.
The parts of aluminium to be welded must be heated up to a maximum of 176 degrees and then processed by setting rather low amperages on the welder as it is a metal with high thermal conductivity.
Finally, the welding speed must also be fairly low because aluminium, being a light metal, can pierce if you stop too long over a welding point (this is all the more true for thin aluminium sheets).
Deca Mastrotig Welder for Aluminium TIG welding on aluminium frame
Not all TIG welders suitable for aluminium come with all the necessary components, and it is often necessary to purchase the appropriate kit because there are different nozzles that need to be used on the welder torch.
3. Aluminium MIG wire welding
Here, too, we recommend that you read the main purchasing guide to better understand the functioning of MIG wire welders.
In addition to a suitable welding machine, aluminium can also be welded with the following equipment:
- aluminium wire reel
- a special kit consisting of wire liner, wire guide roller and nozzles
Telwin Telmig 250/2 Welder for Aluminium Aluminum welding kit
In this case, therefore, the welding filler material will be consumable aluminium wire. MIG welding also involves the use of Argon gas, and even with this method it is necessary to clean the aluminium parts to be welded as described above and heat the foils evenly to a maximum of 176 degrees.
Low amperage and low welding speed are always recommended to avoid making the mistake of piercing aluminium foils.