A comprehensive guide to purchasing welding machines, to help you find the best model for your purposes.
The Complete Guide to help you choose the Best Welding Machine
by the Real Experts of Equipment for Repairs and DIY Activities
Every DIY enthusiast knows the importance of the art of welding. The welding machine is the main tool for hobby DIY, but it also has many applications in the professional field (i.g. in the automotive sector, workshops, body shops and much more).
Whether it is for small domestic maintenance work or other tasks, the welding machines turn out to be essential when using metallic materials. Obviously, the welding techniques to be adopted and the models of welders to be used vary according to one’s work requirements. Finding your way around the world of welding is no trivial matter, but with this purchasing guide to the best welding machine we will try to set you on a simple and clear path to the model best suited to your needs. First of all, it is necessary to clearly assess the purpose and frequency of use of our welding machine.
CONTENTS
1. Introduction
For frequent and prolonged use, it is always recommended to use a reliable and long-lasting welding machine model; we are talking about semi-professional or hobby made in Italy products of well-known brands (such as Telwin and Deca). When purchasing a welding machine, the important thing is not to save money, although many Italian models can be found at very low prices. Making a right investment will be important both in terms of the results of your work and the safety of the product itself.
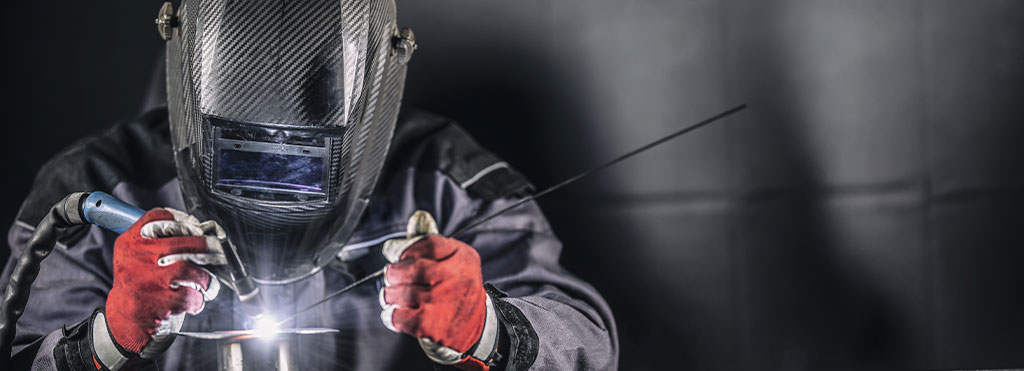
If, on the other hand, the tool is used very little and occasionally, it is also possible to choose a less expensive welding machine, but it is always important to move towards new models or, in any case, ones that have been released in recent years, which is fundamental because safety devices are constantly evolving at a technological level.
Inverter welding machines, which we will discuss in more detail below, are the ideal choice for hobby and DIY work. Their advantages lie in their compact size, low weight and safety for the operator. These are more modern and also slightly more expensive than traditional transformer welders, but they are now much more efficient and are now very popular on the market.
Last but not least, remember to always wear hand and eye protection, and that these must be up to standard!
2. Transformer welders or inverter welders?
This question is at the centre of a major debate among welding enthusiasts and professionals. The dry answer in most cases would be… “it depends…” But behind this simple answer there are much more complex considerations. First of all, it must be said that the inverter system is one of the most important technological development in the field of welding, so we just have to understand the pros and cons of the two types of machines: transformer welders or inverter welders.
After the Second World War, the industrial world experienced a boom in the welding sector. Transformer welders began to show signs of inefficiency due to their heaviness in shipbuilding etc. It wasn’t until the late 1980s with the development of electronics and software that it was discovered that software-controlled inverters could be an excellent solution for welding, opening up a new era in welding. Initially, many machines were characterized by reliability issues and were challenged regarding user interfaces, heat dissipation and problems caused by humidity. But since the early 2000s, inverter welders have literally flooded the market thanks to their versatility and ability to control the welding arc.
Here is table listing the strengths and weaknesses of the two technologies, which we will be explained in more detail later:
Features: | Transformer | Inverter |
---|---|---|
Reliability | ✔ | ❌ |
Versatility | ❌ | ✔ |
Lower weight | ❌ | ✔ |
Quality of the welding arc | ❌ | ✔ |
Cost | ✔ | ❌ |
Lower energy consumption | ❌ | ✔ |
Lower maintenance costs | ✔ | ❌ |
- Reliability is a key feature of an ongoing debate. The history of transformer welders is much longer than that of inverter ones and they have therefore undergone much more evolution in terms of reliability, and are also structurally more robust machines. So, in general we can say that transformer welders are more reliable than inverters, even if the gap is narrowing from year to year.
- Inverter welders are certainly more versatile of traditional transformer machines. Thanks to their technology, inverter welding machines make it possible to adjust almost all the electrical variables that affect welding efficiency, and different welding techniques can be combined in a single machine, providing absolute versatility.
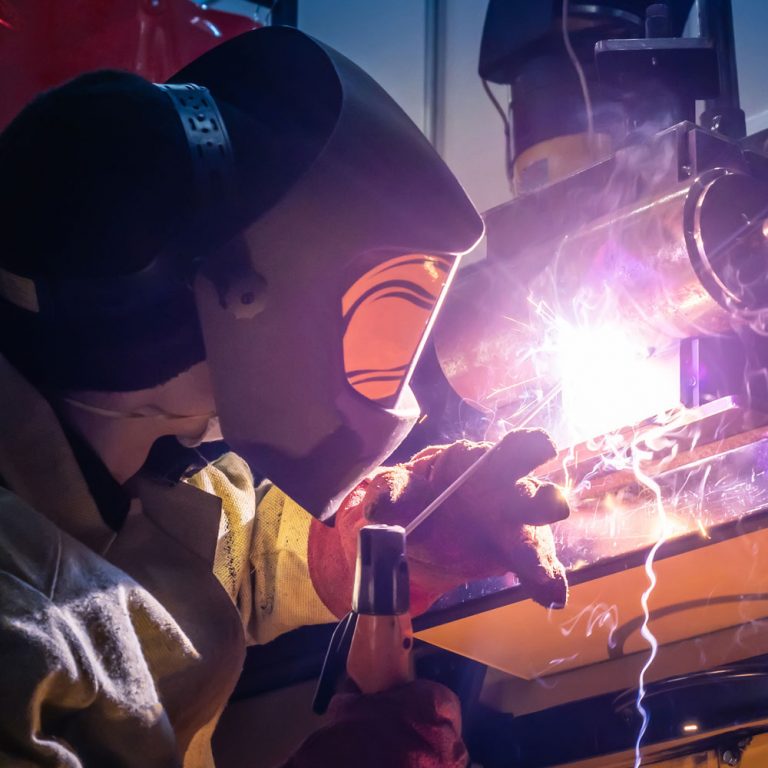
- Inverter welders are also significantly lighter than conventional transformer welding machines. This makes them portable, more comfortable and easier to use, even by less experienced welders.
- The quality of the welding arc is crucial because it naturally affects the quality of the result obtained. If your welding work is limited to domestic tasks on mild steel only, a transformer machine will do just fine. But for a better welding result in all positions and on different materials what is needed is the versatility and efficiency of an inverter welding machine.
- Until a few years ago, inverter machines were much more expensive than others, due to the costs of the new technology. In the last 10-15 years, however, inverter welders have started to be produced on a large scale and the costs are now almost on the same level as transformer welders.
- Inverter welding machines consume less electricity than transformer ones. On the other hand, maintenance costs are higher for inverter welders as they are more complex machines.
This is why we can find transformer machines and inverter machines for all types of welding. For example, for the most common welding method, electrode welding, which we will discuss in more detail in the next section, we can easily identify:
MMA electrode transformer welders MMA electrode inverter welders
3. MMA electrode welders
The MMA or electrode welding machine is capable of delivering a high electrical current. MMA welders are equipped with an electrode holder and a ground cable that must be connected to the metal material to be welded. The electrode is a metal rod which creates an electric arc as it approaches the metal to be welded. This electric arc generates such a high temperature that the electrode melts with the base material to be welded.
Electrode holder Ground cable
The electrode consists of two parts:
- a metal core which is the metal melting and welding
- a coating that forms a protective layer against oxidation. This protective layer, known as slag, must be removed as soon as the weld has cooled with a suitable wire brush, usually supplied with the welding machine. Electrodes are therefore consumable parts whose metal composition and diameter vary according to the work to be done.
Coated electrodes Wire brush for weld slag removal
Electrode welding is suitable for small welding works at a hobby or domestic level. We can consider it as the simplest welding method, and therefore ideal for less experienced users. It is generally employed for repairs and non-intensive welding work. However, welding is never a job to be taken lightly, so there are a few things that the welder must bear in mind:
- maintain an adequate distance between the electrode and the base material to be welded by keeping an eye on the constant consumption of the electrode.
- do not bring the electrode too close to the piece of metal to be welded, otherwise the electric arc cannot be generated
In the field of MMA welding, inverter machines are the most prominent as they have many advantages:
- Inverter welders are more light and compact
- the result obtained is of better quality thanks to a more accurate adjustment of the welding current
- are equipped with state-of-the-art safety systems.
- Common safety systems
- overvoltage
- thermostatic protection
- undervoltage
- overcurrent
- motor generator (+/-15%): it guarantees the correct operation for variations in supply voltage up to 15%, we recommend that the generators are adequately stabilized.
- This inverter welding machine is equipped with HOT START system, a boost of additional power that facilitates arc striking, in case of electrodes that are difficult to strike.
- Also equipped with an ANTI-SICKING device, to easily detach the electrode if it remains glued to the piece
- Furthermore, when the welding arc is short, the ARC FORCE system increases the Amperes.
Many inverter electrode welders are capable of TIG welding by purchasing the specific torch. Hybrid models of inverter MMA + TIG welders are very common.
TIG welding will be discussed in more detail in the following section.
4. TIG welders
TIG welding is the most aesthetically pleasing, high-quality welding method, which is why it is used in cases where the welding is left visible, such as bicycle frames.
The TIG function creates a weld seam that looks as if it were made up of many small coins stacked on top of each other.
TIG stands for Tungsten Inert Gas. TIG welding creates an electric arc between the base metal material and a non-consumable tungsten electrode. Such welding can be carried out with or without filler metal. The biggest advantage of TIG welding is that you can weld any metal and the results are always of high quality. Another feature is that the filler material is disconnected from the heat input in the weld unlike MMA or wire welding.
TIG welding TIG welded bicycle frame
TIG welders are inverter driven and can be manual or semi-automatic. They are more complex machines than electrode inverters, as there are many parameters to consider in order to obtain the best welding result.
This type of welding is used for fine and particularly accurate work: TIG allows cleaner welds with an almost total absence of slag.
On the other hand, this more professional welding technique is not suitable for beginners and requires a much higher level of experience and concentration than electrode or wire welding. TIG welding also requires more working time and operates at a lower current. The welder’s coordination is very important, the movements of the torch and the addition of metal must be accurate and precise, and the foot can often be used to control the current with a foot pedal.
There are many parameters to consider:
- spatters intensity
- preparation of tungsten
- pulsation
- ascending and descending curve
- background current
- peak intensity
- power frequency
TIG welders are highly appreciated because they guarantee high quality welding. They are used in the welding of thin sheets or in the execution of airtight welding jobs. Furthermore, the deposition rate of TIG are the lowest in its class, which is why TIG is the most widely used type of welding in the aerospace industry, where quality matters far more than production costs.
In addition to a suitable inverter welding machine, other elements for TIG welding are:
- TIG torch
- Tungsten electrodes
- Gas cylinder
TIG torch Tungsten electrodes Gas cylinder
The TIG torch is connected to the gas cylinder by means of a special tube. In fact, the TIG torch consists of:
- Ceramic cap
- Electrode holder nozzle
- Knob
- Gas cylinder connection tube
The cap serves to adjust the gas flow and can be unscrewed quite simply. The size of the cap to be attached to the torch is chosen according to the welding width to be carried out. In the welding rod holder pen there is the electrode holder nozzle in which the suitable electrode in inserted: these can vary in diameter from 0.25 to 6.4 mm. Finally, the knob is used to turn on the gas in order to start welding.
TIG inverter welders can be of two types:
- Direct current
- Alternating current
The former are simpler machines and can be used to weld iron, copper, stainless steel, zinc etc.
If, on the other hand, you want to weld more special materials such as aluminium, bronze and magnesium, you need more professional and complex machines such as those that allow you to choose between alternating current and direct current welding, directly from the display of the welding machine’s control panel: we are talking about TIG AC/DC welders.
TIG DC welding machine Deca TIG AC/DC Welder Control panel
5. Wire welders
Wire welding is called continuous wire welding because the welder features a coil of metal wire on the inside, which is unwound and consumed and provides the filler material. Wire welders can be found on the market with both transformer and inverter technology, performing the same functions:
Telwin Transformer Wire Welder Awelco Inverter Wire Welder
Wire welders are generally called MIG/MAG welding machines as they make use of a gas to protect the weld seam. Gas wire welders are the most widespread on the market. This gas propagates from the MIG torch during welding work.
- MIG (Metal Inert Gas) welding: argon gas is used for stainless steel, aluminium and non-ferrous metals
- MAG (Metal Active Gas) welding: a mixture of argon and carbon dioxide is used, suitable for welding carbon steels.
Wire welding is a fairly intuitive welding technique that is also suitable for less experienced welders. Although the quality of the result obtained is one of its strong points, unlike electrode welding for example, it is less practical in terms of transportability and the number of elements required for the work.
In fact, to carry out a wire welding operation, it will be necessary to connect the MIG/MAG welder to a gas cylinder. The gas has the function of protecting the weld from oxidation, rather like the coating of the electrode in MMA electrode welding.
Another negative aspect is that this type of welding is not suitable for outdoor work as the wind can interrupt operations.
MIG/MAG torch Steel wire reel Argon and CO2 gas cylinder
- Also very popular are no gas wire welders. They have a much simpler construction and the practical advantage of not requiring a gas cylinder, as well as being less expensive than MIG/MAG machines.
With NO GAS wire welders it is necessary to use SELF-SHIELDED WIRE instead of solid metal wire. The self-shielded wire has a powder which is released during the welding process and creates a gaseous layer that serves to protect the weld from oxidation.- ADVANTAGES:
Less expensive machines than MIG
No gas cylinder
More suitable for outdoor work
Stronger welds with thicker work parts - DISADVANTAGES:
Self-shielded wire is more expensive than solid wire
Lower quality welds (“less aesthetically pleasing”)
Not suitable for welding smaller and thinner material
- ADVANTAGES:
Stanley MIKROMIG No-gas Wire Welder Self-shielded wire reel
The wire welding machines have a side door through which the basic components of the machine can be accessed:
- Wire reel
- Wire feeder roller
- Polarity +/-
It is important to pay attention to the setting table.
The settings essentially concern the amperage and the wire speed: these two units are positively correlated in that as one increases, the other increases and vice versa.
Inside of the wire welder Main components of the wire welder Amperage adjustment
When using gas, press the button on the MIG torch which starts the wire feed. Then it is important to adjust the gas supply valve, while the controls on the front of the welder can generally be used to set the type of wire size and the thickness of the parts to be welded. It is important that the wire runs at the right feed rate to get a good result. If the wire feed is too fast, it will not have time to fuse properly, and if it is too slow, the welding force will be lost in several spots.
Argon gas welding MIG gas wire welding
6. Multi-process welders
The multiprocess or multi tool welding machine is able to combine several types of welding in one machine. This means that with just one welding machine you can choose between electrode, wire or TIG welding.
These welders, being able to carry out different types of welding, will have specific setting tables for each mode. Generally speaking, multiprocess machines are equipped with the components for MIG/MAG (gas wire) welding: MMA and TIG welding can therefore be carried out by purchasing the appropriate welding kits separately.
They are almost always heavy-duty and large machines. They are microprocessor-controlled and feature also the synergy function: just set the thickness of the material to start welding, furthermore, the smart and automatic control of the arc will maintain maximum performance of the welding phases in all working conditions.
Technomig 215 Dual Synergic Multiprocess Welder Synergy function
7. Other types of welders
- Tin soldering iron is a type of welder that brings the tin metal alloy to the right temperature, i.e. melts the tin so that it is ready for the soldering function.
- The oxy-fuel welders allow the so-called oxyacetylene welding. The main difference with other welding methods is that no power supply is required. They are “outdated” machines that can be found in a few rare workshops. The energy for processing materials is obtained by burning acetylene, a highly flammable gas that comes into contact with oxygen through a blowpipe that also acts as a mixing chamber. There are no single machines capable of performing these functions, but only welding kits.
- Spot welders are used in the industrial sector and therefore belong primarily to the professional sphere. Their name derives from the fact that the welding process is carried out by joining two pieces of metal using stitches, and is used for example to cast sheet metal, but can also be found in the goldsmith’s sector. Metals are melted by electrical discharges generated by two electrodes.
- Plasma welders are a kind of evolution of TIG welding machines and are used in a more industrial environment. Compared to TIG machines, they enable the welding of larger and thicker metals, titanium and nickel alloys, and provide more power and a higher working speed. They prove to be useful for rather high productivity needs, which is why they are mostly used in automotive manufacturing companies.
- Many plasma welders can be presented as 2-in-1 combination machines, and therefore also perform the function of plasma cutting. Plasma cutters are used to cut metal of different thickness.
Tin soldering iron Oxy-fuel welding kit Deca spot welder Telwin plasma system